apro questo thread, che avevo pronto già da novembre ma non ho avuto modo di pubblicarlo prima di stasera, per portare alla luce un problema che alla lunga potrebbe capitare a chiunque abbia un compressore munito di serbatoio.
Come ben sapere l’acqua di condensa è comunemente presente in tutti gli impianti di generazione di aria compressa, in quantità più o meno elevate, in proporzione al volume di aria prodotta ed in funzione della stagione e della zona geografica. Si va da 1 ml per metro cubo (Inverno in zona con clima temperato) fino a superare i 20 ml per metro cubo (zona tropicale).
Il compressore, come tutti sappiamo, comprime l’aria ambientale e di conseguenza comprime tutte le parti che la compongono, compreso il vapore acqueo.
Questo vapore acqueo, una volta introdotto nell’impianto ad aria compressa, tende a condensarsi formando acqua. Inoltre, in questo processo di condensazione, l’acqua si aggrega alla maggior parte degli inquinanti presenti nell’aria e alle micro particelle di olio, rilasciate dal compressore in fase di compressione, dando origine ad un’emulsione che può creare seri problemi, sia all’impianto che alle macchine ad esso collegate.
Tutto questo va gestito in modo opportuno ed il ruolo dei sistemi di scarico della condensa è fondamentale. La condensa è prevalentemente composta da acqua. Negli impianti da compressori lubrificati si aggiungono alla condensa tracce di olio, con concentrazioni anche superiori a 2.000 ppm. Nel caso di impianti da compressori “oil free” non sono presenti oli ma la situazione non è migliore in quanto la condensa che ne deriva ha valori di ph <7 (acidi), con un elevato potere corrosivo.
Considerando poi che l’aria compressa è aspirata dall’ambiente del sito produttivo, nella condensa si aggregano micropolveri ed inquinanti di ogni genere.
L’elevata concentrazione di inquinanti richiede per legge un trattamento di depurazione delle condense che si può delegare ad aziende specializzate nel recupero di liquidi inquinanti oppure dotando il proprio impianto di un separatore acqua/olio a carboni attivi che, trattenendo gli oli e le altre sostanze inquinanti, permettono lo scarico dell’acqua depurata direttamente nella rete fognaria.
La circolazione della condensa nell’impianto è la prima origine di danni o usura anomala delle apparecchiature utilizzatrici di aria compressa, inoltre in alcuni processi produttivi, come ad esempio la verniciatura, i danni non si limitano ai macchinari ma si ripercuotono anche sulla produzione.
Un corretto scarico automatico/manuale dell’acqua di condensa nell’impianto di produzione e trattamento dell’aria compressa permette di aumentare notevolmente l’efficienza delle attrezzature ad esso collegate, limitandone l’usura e la manutenzione.
Esistono in commercio svariati sistemi di scarico della condensa, con differenti tecnologie di funzionamento.
I sistemi più semplici prevedono uno scarico manuale tramite valvolina a vite posta sul serbatoio; altri impianti più professionali prevedono uno scarico automatico: un circuito temporizzatore comanda alternativamente l’apertura e la chiusura di un’elettrovalvola, in funzione dei tempi di pausa/lavoro imposta sull’apposito pannello di programmazione. Questi sistemi richiedono una regolazione periodica dei tempi di scarico in funzione della stagione ma questo ovviamente non è il nostro caso.
Non esiste una regola per calcolare l'accumulo di condensa all'interno del nostro impianto che lega il tempo di funzionamento, perché potrebbe essere suscettibile a fattori ambientali e climatici diversi da utenza a utenza, dal momento che il tasso di umidità varia durante l'anno, alternando periodi freddi e secchi a periodi caldi e umidi.
Come già detto la condensa è vapore acqueo condensato che ha valori di ph <7 (acidi), quindi con un elevato potere corrosivo. I serbatoi destinati all'immagazzinamento e distribuzione di aria compressa più diffusi sul mercato sono costituiti da acciao al carbonio, ma non è difficile trovarne alcuni anche abbastanza costosi interamente in acciaio inox.
Che differenza c'è tra acciai al carbonio ed acciai inossidabili?
La differenza sta nella composizione chimica, infatti gli acciai inossidabili hanno un contenuto di cromo di almeno il 10,5%. Nel settore industriale gli acciai inossidabili normalmente utilizzati hanno un contenuto di cromo superiore a questa soglia (solitamente il 18%) e contengono inoltre nickel, molibdeno ed altri elementi. La presenza del cromo è, come già detto, importante per la formazione dello strato passivato resistente alla corrosione, mentre il nickel contribuisce a migliorare le caratteristiche meccaniche. In generale si può dire che gli acciai inossidabile sono più resistenti alla corrosione ed hanno migliori caratteristiche meccaniche rispetto agli acciai al carbonio.
L'acciaio al carbonio (ferro) è il materiale più soggetto ad arrugginimento ed il più economico tra i più comuni materiali forati. Il carbonio ha un duplice effetto sugli acciai legati temprabili. Esso infatti controlla la massima durezza ottenibile e contribuisce sostanzialmente alla temprabilità. L’aggiunta di carbonio è il metodo meno costoso per ottimizzare la temprabilità. Ai normali acciai al carbonio non vengono aggiunti intenzionalmente altri elementi. Essi sono generalmente utilizzati per le applicazioni meno critiche in ambienti non corrosivi, e di solito non sono trattati termicamente. Fatta eccezione per gli acciai per molle e cuscinetti, si usa raramente una percentuale di carbonio superiore allo 0,60 per cento nelle parti lavorate. L'acciaio al carbonio viene prodotto in lamiere o nastri che vengono spianati sino allo spessore desiderato mentre il materiale è ancora caldo o subito dopo il suo raffreddamento.
Le differenze nel processo produttivo influenzano il costo, la qualità e le proprietà meccaniche. A titolo di esempio e completezza riporto alcune lavorazioni:
Questo argomento vuole porre l'accento su un aspetto molto importante che è la sicurezza verso noi stessi e chi ci circonda nell’utilizzare compressori dotati di serbatoio: difatti ogni volta che un oggetto, in questo caso un serbatoio, viene sottoposto a ripetuti cicli di lavoro con forze alternate di segno opposto, si creano micro deformazioni elastiche che in condizioni di materiale esente da difetti non generano alcun problema alla struttura interna del materiale perché si sta operando in campo elastico. Se la struttura interna del materiale inizia a corrompersi a causa di alterazioni dovute ad agenti esterni quali la ruggine che ne consuma la struttura, o difetti superficiali dovuti alla lavorazione del materiale, le deformazioni passano dal campo elastico a quello plastico instaurando la fatica oligociclica caratterizzata da deformazioni plastiche alternative di segno opposto. Questo fenomeno si verifica in materiali metallici e dà luogo a rapida rottura dopo 50.000-100.000(stime approssimative e suscettibili di a molte variabili) cicli a causa del propagarsi di fessure o cricche che si innescano in superficie per i ripetuti corrugamenti di tipo plastico. E' un pò quello che avviene, con le opportune limitazioni e semplificazioni del caso, ad un palloncino dopo che è stato gonfiato e sgonfiato innumerevoli volte oppure, ancor meglio, a quello che avviene alle fusoliere degli aerei di linea sottoposte a numerosi cicli di pressurizzazioni e depressurizzazioni.
Questo fenomeno è reso ancor più accentuato se consideriamo che il potere corrosivo dell'acqua aumenta in condizioni di pressioni elevate generando così una vera associazione a delinquere costituita da fatica+corrosione+cattiva manutenzione.
Se trascuriamo questi aspetti, nel serbatoio, all'oscuro e lontano dallo scorrere frenetico della umana vita quotidiana con ritmi e preoccupazioni di tutt'altro genere, la sinergia esistente tra questi fenomeni darà vita a una drammatica scalata verso un'esplosione incontrollata. Ciclo dopo ciclo inizierà a formarsi una vera e propria bomba ad orologeria, caricata ad aria e particelle metalliche, posta a pochi palmi da noi e di chi ci sta intorno. Quando anche l'ultima tenace e inutile resistenza dell'acciaio sarà capitolata, un'onda d'urto unita a proiezioni di scorie metalliche ad alta velocità ci investirà quando meno ce l'aspettiamo dilaniando non solo il serbatoio ma anche quello che doveva essere un semplice e innocuo passatempo.
Se si volesse fare un parallelo con fenomenologie di proporzioni macroscopiche si potrebbe prendere come esempio il caso del volo Aloha Airlines 243 ove causa ed effetto sono molto somiglianti a quanto riportato sopra.
Siete ancora scettici?
Nelle immagini di seguito viene mostrato l’interno di un serbatoio a forma di parallelepipedo, deputato a immagazzinare aria compressa a 8 bar, che ha avuto una cattiva manutenzione.
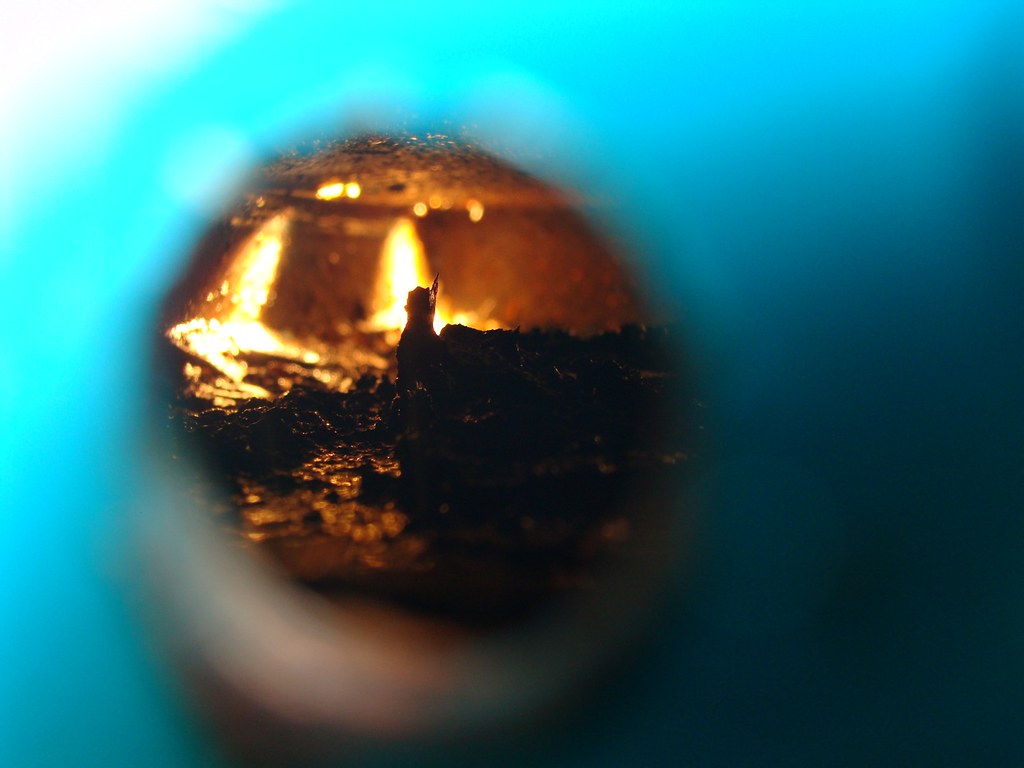
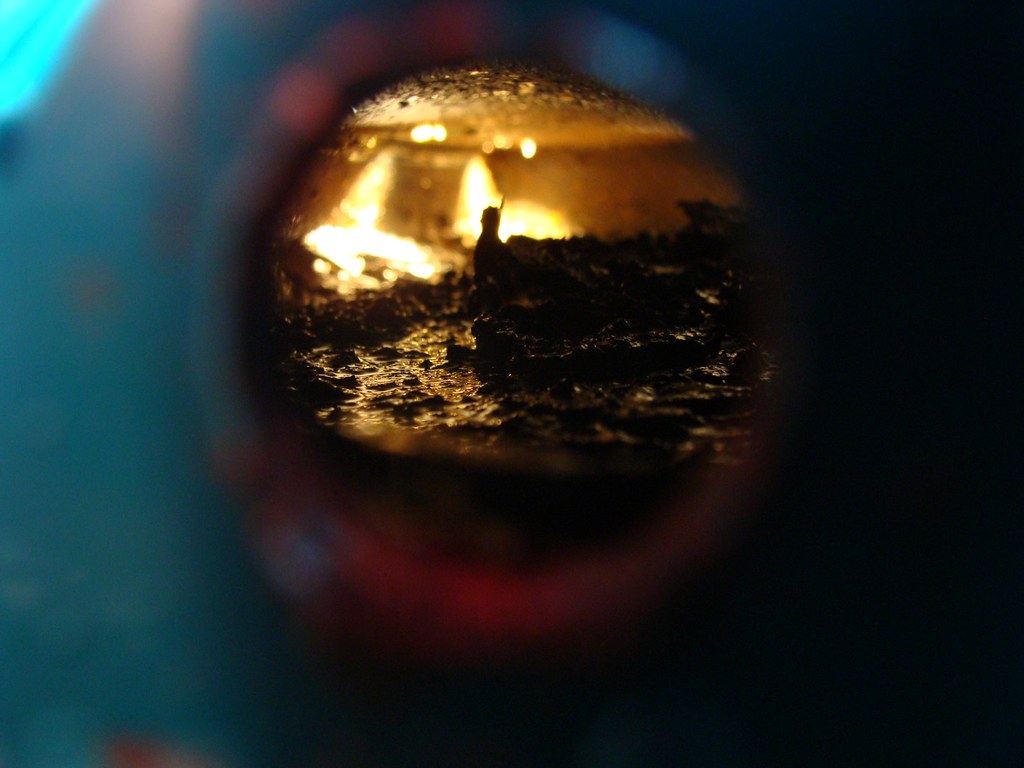
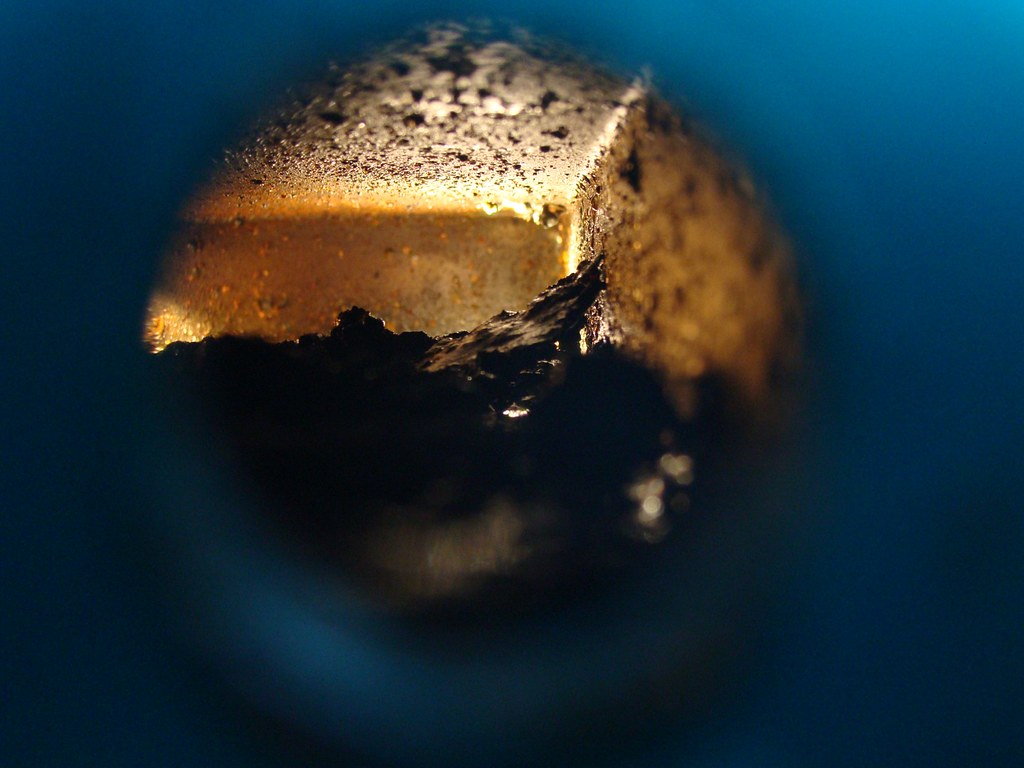
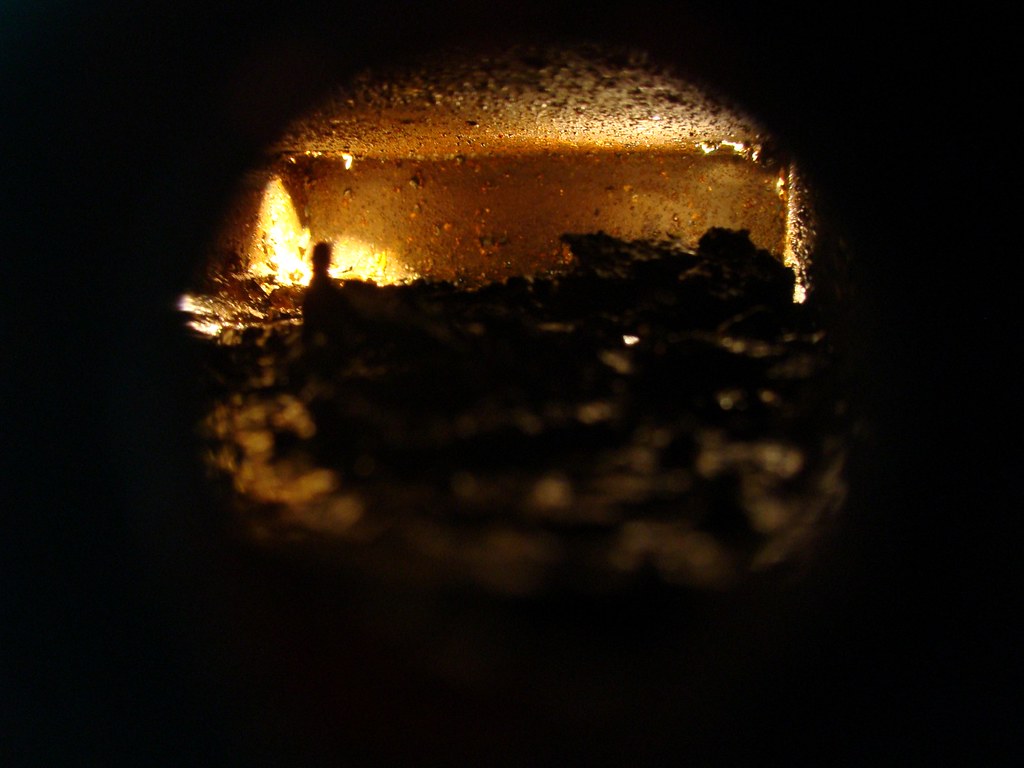
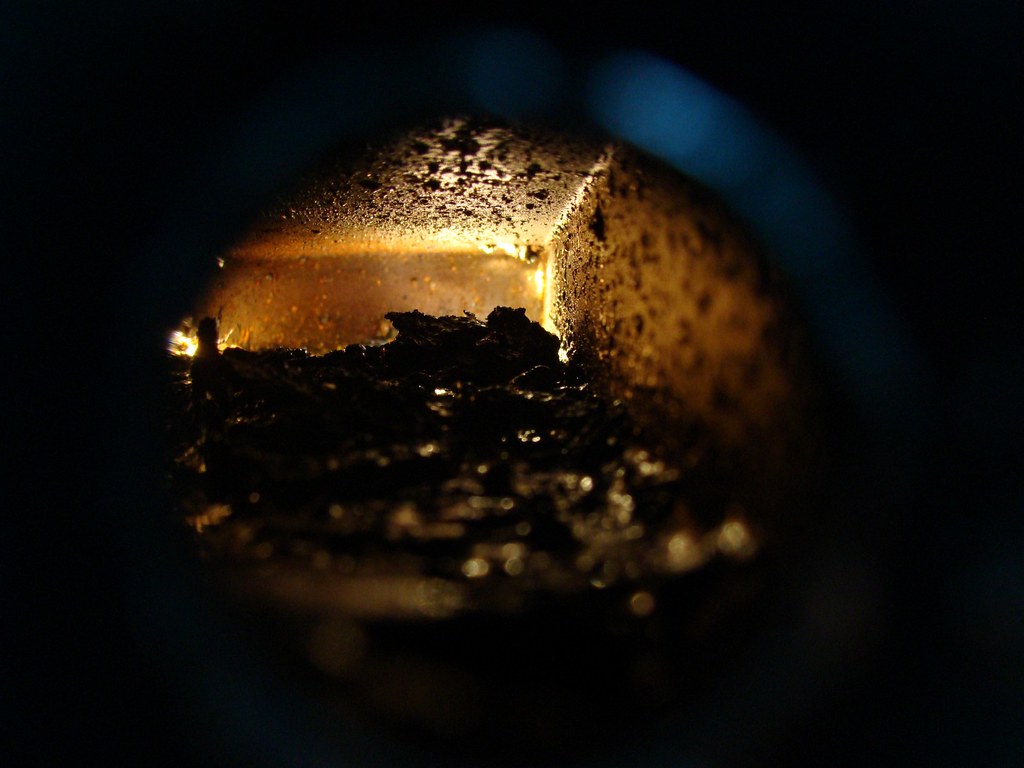

Nelle foto, scattate alla meglio, si possono notare le superfici laterali e superiore compatte e integre anche se vi è comunque presenza di ruggine in modeste quantità.
La superfice inferiore, invece, appare molto rovinata e irregolare a partire dagli spigoli laterali sino a invadere tutta la zona centrale del pannello inferiore. Come si nota dalle immagini, in alcuni punti sono presenti scaglie metalliche separate, zone rialzate in sacche localizzate e aree dove il materiale è mancante.
Tutto il pannello inferiore è pesantemente compromesso e del tutto irrecuperabile. La corrosione ha raggiunto livelli così profondi che ha devastato la struttura interna dell’acciaio facendolo gonfiare e sfogliare in sottilissime lamine, generando uno stadio tale da far curvare il pannello compromesso già a una pressione di 5 atm sulle 8 a pieno carico. Non saprei dire quanta vita residua ancora da percorrere sarebbe rimasta prima del botto ma credo ancora poco e al di fuori dei parametri di sicurezza.
La prova del nove è arrivata dando piccoli colpi al serbatoio e inclinandolo sul lato forato per tirar fuori scaglie metalliche di varia grandezza e di varia consistenza.
Queste sono solo alcune di quelle venute fuori dall’angusta apertura, altre di dimensioni maggiori sono ancora all’interno.
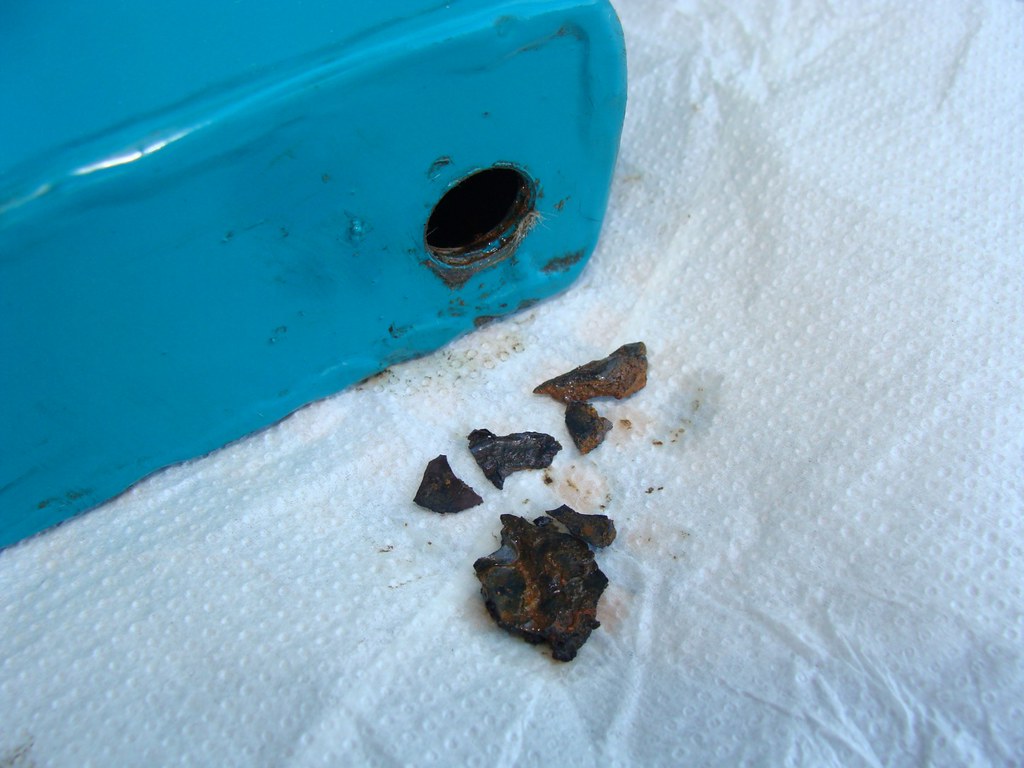
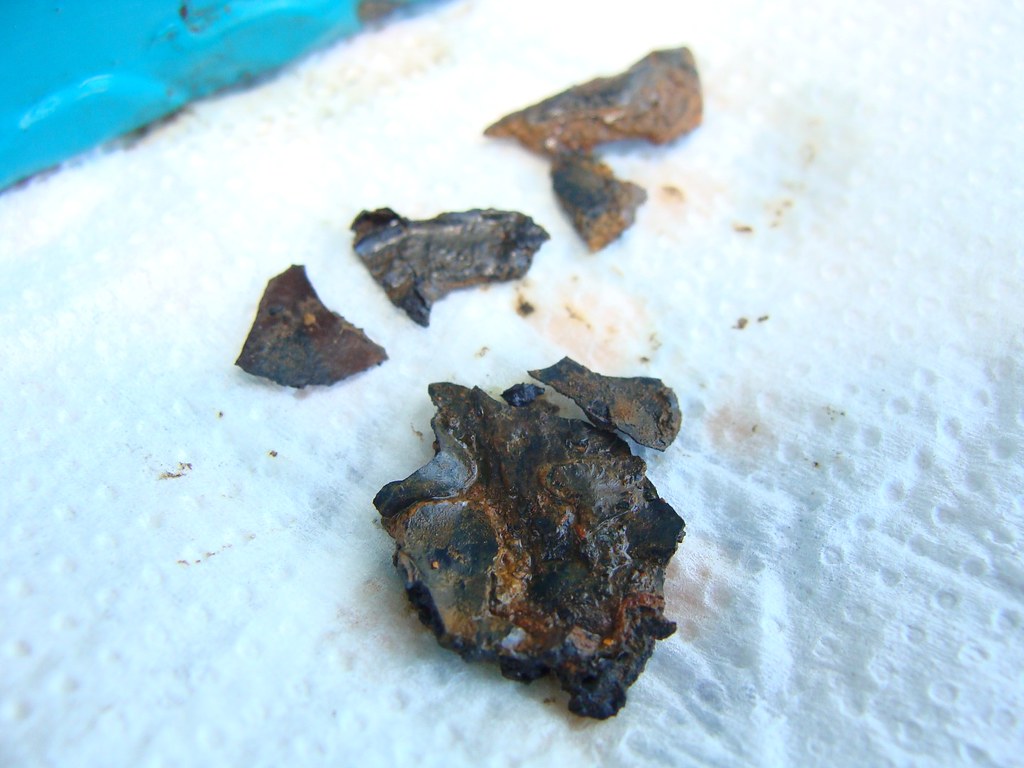
Provate a immaginare cosa sarebbe venuto fuori se tutti gli 8 Kg per cm^2 avessero squarciato la parete…
Cosa fare per difenderci?
Bhè, prima di tutto chiedere e informarsi sul tipo di materiale con cui è costruito il serbatoio e se il costruttore ha previsto un trattamento interno, tipo zincatura a caldo atta a preservare il serbatoio dalla ruggine e soprattutto se sul serbatoio è riportata la targhetta che ne attesti il collaudo secondo le direttive europee. Qualora non fosse possibile risalire alle prime due informazioni(tipo di materiale e trattamento) sconsiglio lavaggi interni con prodotti che favorirebbero la corrosione o trattamenti artigianali che altererebbero la struttura cristallina del materiale. Nell’ultimo caso…lasciate il compressore lì dove si trova!
Se una leggera patina di ruggine è presente all’interno (cosa abbastanza fisiologica) si può pensare di applicare un prodotto chiamato convertitore di ruggine reperibile in ferramenta e seguire quanto descritto sulle istruzioni, avendo cura che tutte le zone interne siano interessate dal prodotto. Per far questo vi consiglio di liberare il serbatoio da ogni raccordo e attacco presente su esso prima del trattamento. Questo però non è sufficiente, o meglio basta ma dovremmo impegnarci a fare qualcosa in più intervenendo sulle nostre abitudini: svuotare a fine sessione il serbatoio dall’aria e dall’acqua di condensa che si è formata dall’apposita valvolina di sfiato, lasciando completamente aperto il condotto sino alla prossima sessione di utilizzo per permetterne l’evaporazione. Ove possibile (compressori oil-less) , staccare anche il tubo di mandata aria che dal motore arriva al serbatoio per una più completa areazione.
Evitate in ogni caso di chiudere la seduta di modellismo con il serbatoio carico d’aria o di condensa; seppur poca crea ugualmente danni profondi anche al motore alle membrane dello stesso.
Costruirsi degli impianti di aria compressa con materiali di recupero avvalendosi di tutorial trovati in rete è una cosa che va fatta con molta cautela. Se da un lato questa cosa è molto affascinante e stimolante l'invito è quello di sapere bene cosa si sta facendo evitando di utilizzare serbatoi sprovvisti di scarico condensa, ancora più se non siete certi della loro integrità. Le bombole degli estintori vuoti o quelle da immersione subacquea vengono spesso utilizzate a mò di serbatoio in queste autocostruzioni, sottovalutando il loro reale utilizzo rispetto agli usi impropri che ne vengono fatti.
Queste bombole, nonostante siano in grado di resistere a elevate pressioni che vanno oltre i nostri interessi, a differenza dei serbatoi da compressore, hanno un'unica via per l’ingresso e l’uscita dell’aria. Il rischio di accumulare agenti corrosivi e non poterli espellere con regolarità è alta, perché sprovvisti di un’uscita ausiliaria dedicata a far defluire la condensa. Il rischio di ritrovarsi una bomba ad orologeria sotto la scrivania come nel caso del serbatoio di cui sopra è meglio evitarla sempre così come l’eventualità di ritrovarsi prematuramente su una nuvoletta a cantare "Nel blu dipinto di blu".
Prima di tutto badiamo alla sicurezza e alla salute.
Ciauz
